How to upgrade Tyre Pyrolysis Carbon char into rCB
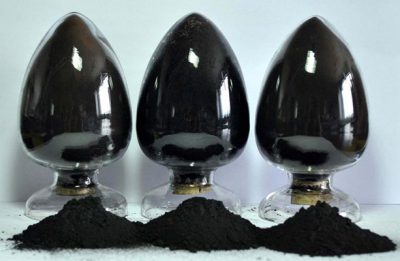
Recycled Carbon Black (rCB) is a sustainable material produced by processing carbon-rich waste such as end-of-life tires and rubber products. Its production primarily relies on pyrolysis technology: under high-temperature (500–800°C) decomposition in an oxygen-deprived environment, organic components in waste tires are thermally cracked into carbon black, oil, and gas. Subsequent purification, sieving, and grinding processes refine the raw pyrolysis residue into high-purity rCB.
The Rising Demand for Sustainable Carbon Black Recycling
With global tire production exceeding 1.8 billion units annually, end-of-life tires (ELTs) generate over 30 million tons of carbon black-containing waste. Recovered carbon black (rCB) has emerged as a critical material for circular economy initiatives, offering:
- Resource conservation: Reduces reliance on virgin carbon black production (~2.7 tons CO₂ emitted per ton of virgin CB)
- Cost efficiency: rCB production costs 40-60% lower than virgin alternatives
- Environmental compliance: Meets EU Tire Recycling Directive (2006/12/EC) and EPA emission standards
Key Challenges in rCB Processing
1. Material Complexity
- Variable feedstock composition (15-35% carbon content in ELT-derived pyrolyzed char)
- Contaminant removal requirements (ash <8%, volatile matter <2% for premium grades)
2. Precision Particle Engineering
- Target particle size: D97 ≤5μm for high-value rubber compounding applications
- Narrow particle distribution (Span value <1.2) for optimal dispersion
3. Energy Efficiency Demands
- Conventional mills consume 120-150 kWh/ton for sub-10μm grinding
- Thermal degradation risks above 80°C processing temperatures
Integrated Processing Solution
Stage 1: Pre-Treatment System
Process | Key Parameters | Equipment Example |
---|---|---|
Deagglomeration | Initial size reduction to <5mm | Hammer Mill (0-3mm output) |
Magnetic Separation | Fe removal efficiency >99.5% | Overbelt Magnetic Separator |
Thermal Purification | 450-600°C in oxygen-free atmosphere | Rotary Calciner |
Stage 2: Core Grinding Technology
Technical Superiority for rCB Processing
- Precision Size Control
- Achieves D97 ≤5μm (2500 mesh) through vertical turbine classifier
- ±0.5μm particle size stability via automatic feedback system
- Energy-Efficient Operation
- 30% lower energy consumption vs. jet mills (85-100 kWh/ton at 5μm)
- Patented multi-layer grinding mechanism reduces over-processing
- Advanced Material Handling
- Special alloy grinding rollers (HRC 62-65) withstand abrasive CB particles
- Gas-tight system prevents oxidation (O₂ content <50ppm)
Model Selection Guide
rCB Capacity | Recommended Model | Power Consumption | Footprint |
---|---|---|---|
0.5-4.5 t/h | XZM221 | 75kW | 8.5×4.2m |
2.5-14 t/h | XZM244 | 185kW | 12.1×5.8m |
5-25 t/h | XZM268 | 315kW | 18.3×7.6m |
Stage 3: Post-Processing Optimization
- Surface Modification: Silane coupling agent coating (0.5-3% loading)
- Quality Assurance: Laser particle analyzer + BET surface area testing
- Packaging: Nitrogen-filled big bags (500-1,000kg capacity)
Case Study: Tire Manufacturer Success Story
Client Profile: European tire producer targeting 30% rCB incorporation
Implementation Results:
- Achieved 5.2μm median particle size (D90=7.8μm)
- 92% energy saving vs. previous ball mill system
- Production cost reduction: €185/ton
- Certified to REACH Annex XVII compliance
Future-Proof Your rCB Operation
The XZM Ultrafine Mill series delivers three critical advantages for carbon black recyclers:
- Market competitiveness: Produce ASTM D6556-compliant rCB grades
- Operational flexibility: Adjust fineness from 325-2500 mesh
- Sustainability leadership: 75dB noise level and <20mg/m³ dust emissions
For plants processing >3 tons/hour of pyrolyzed carbon black, the XZM268 model demonstrates:
- 18-month ROI through energy savings and premium product pricing
- 98% operational availability with modular wear part replacement
Next-Step Recommendation
Contact our engineering team for a free Material Test & Process Simulation – optimize your rCB quality parameters while verifying capacity requirements.
XZM Ultrafine Mill: Transforming Carbon Black Recycling Economics Through Precision Grinding Technology