Limestone Powder Preparation Equipment for Power Plant Desulfurization
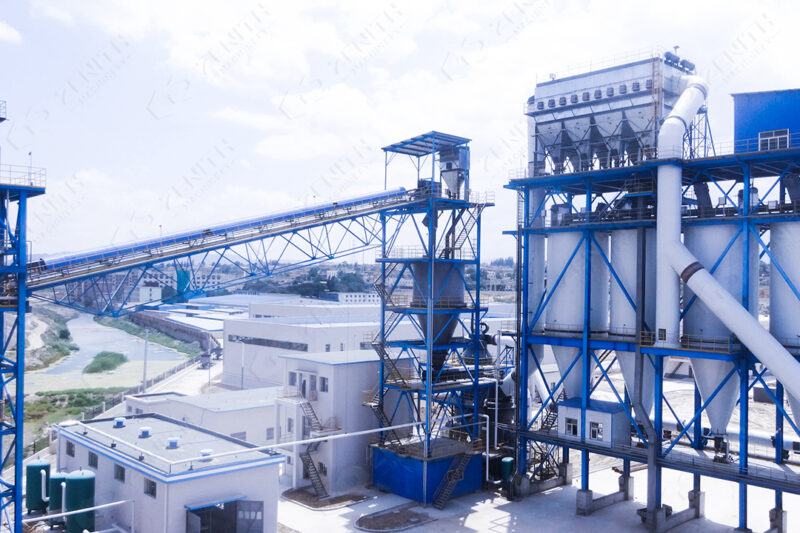
Introduction to Flue Gas Desulfurization (FGD) Technology
Modern coal-fired power plants rely heavily on limestone-based wet flue gas desulfurization (WFGD) systems to meet stringent emission regulations. The efficiency of SO2 removal directly correlates with the quality of limestone powder, where particle size distribution and reactivity play decisive roles. Typically, limestone powder for WFGD requires 90% of particles to pass through 325 mesh (45μm) with optimal CaCO3 content exceeding 90%.
Key Requirements for Desulfurization Limestone Powder
- Particle Size: D90 ≤ 44μm (325 mesh)
- Chemical Composition: CaCO3 ≥ 90%, MgCO3 ≤ 2%
- Moisture Content: ≤ 1% for dry systems
- Reactivity: Complete dissolution within 4 minutes in pH4 acidic solution
Critical Equipment Selection Criteria
When selecting limestone grinding equipment for power plant desulfurization, operators must evaluate:
1. Grinding Efficiency
The equipment should achieve target fineness with minimal energy consumption. Vertical roller mills typically consume 18-22 kWh/t for 325 mesh products, significantly lower than traditional ball mill systems.
2. System Reliability
Continuous operation demands equipment with:
- Wear-resistant grinding components (60HRC minimum)
- Automatic lubrication systems
- Failsafe mechanisms for power fluctuations
3. Environmental Compliance
Modern mills must integrate:
- Pulse jet bag filters with ≤20mg/Nm³ emission
- Noise control below 85dB at 1m distance
- Zero wastewater discharge designs
ZENITH’s Recommended Solutions
With over three decades of mineral processing expertise, ZENITH offers cutting-edge grinding technologies specifically optimized for power plant desulfurization applications.
1. MTW Series Trapezium Mill
Our MTW215G model demonstrates exceptional performance in limestone preparation:
- Capacity: 15-45 t/h of 325 mesh powder
- Energy Efficiency: 22% lower power consumption than industry average
- Key Innovation: Curved air duct design reduces pressure loss by 15%
- Maintenance Advantage: Quick-change modular grinding rollers (4hr replacement time)
2. XZM Ultrafine Mill
For plants requiring finer particles (D97≤5μm), our XZM268 provides:
- Precision Classification: Turbo air classifier with 99% separation efficiency
- Compact Footprint: 40% space saving versus conventional systems
- Smart Operation: PLC-based automatic fineness adjustment
- Case Study: Achieved 98.7% SO2 removal at Guangdong Taishan Power Plant
Technical Comparison Table
Parameter | MTW215G | XZM268 | Ball Mill |
---|---|---|---|
Output Fineness | 325-2500 mesh | 325-2500 mesh | 325-400 mesh |
Power Consumption | 22 kWh/t | 28 kWh/t | 38 kWh/t |
Noise Level | ≤82dB | ≤75dB | ≥95dB |
Maintenance Cycle | 8,000 hours | 10,000 hours | 3,000 hours |
System Integration Approach
ZENITH provides complete limestone preparation systems including:
1. Raw Material Handling
- Vibration feeders with metal detection
- Automatic moisture compensation
- Pre-crushing to ≤20mm
2. Grinding Process Control
- Online particle size analyzers
- AI-based production optimization
- Remote monitoring via ZENITH IoT platform
3. Product Conveyance
- Dense phase pneumatic transport
- Anti-segregation silo designs
- Automated truck loading
Why Choose ZENITH?
Our competitive advantages include:
1. Engineering Expertise
With 5 professor-level engineers and participation in 8 national standard formulations, we deliver technically superior solutions.
2. Global Support Network
30+ overseas offices ensure:
- 4-hour response time for critical issues
- Local spare parts inventory
- Onsite training programs
3. Performance Guarantee
All our desulfurization grinding systems come with:
- 12-month comprehensive warranty
- Lifetime technical support
- Guanteed production capacity
Selecting proper limestone preparation equipment significantly impacts WFGD system performance and operating costs. ZENITH’s MTW and XZM series mills offer power plants reliable, high-efficiency solutions with industry-leading technical support. Contact our engineering team today for customized system design based on your specific fuel sulfur content and emission requirements.