Energy-Saving Retrofitting Services for Ore Grinding Mills: Reduce Costs & Boost Efficiency
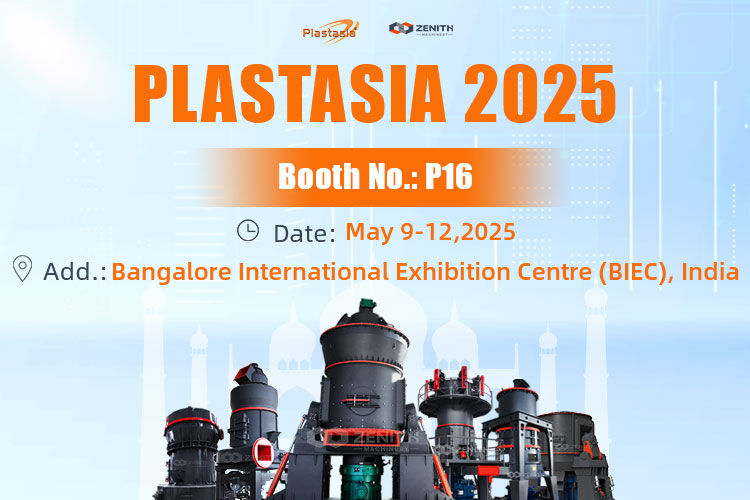
In today’s competitive mining industry, optimizing ore grinding operations is crucial for maintaining profitability. Energy consumption in grinding circuits typically accounts for 40-60% of total mineral processing costs, making energy-efficient retrofits one of the most impactful operational improvements. ZENITH, with over 30 years of experience in grinding technology innovation, offers comprehensive retrofitting solutions that deliver measurable reductions in power consumption while increasing throughput capacity.
The High Cost of Inefficient Grinding
Traditional grinding mills often suffer from:
- Excessive energy consumption (15-50 kWh/t)
- Low material utilization rates (typically 60-75%)
- Frequent maintenance requirements
- Suboptimal particle size distribution
Our Retrofitting Methodology
1. Comprehensive System Assessment
Our engineers conduct thorough evaluations including:
- Power consumption analysis
- Material flow testing
- Wear pattern examination
- Process bottleneck identification
2. Precision Engineering Solutions
We implement targeted upgrades such as:
- Advanced liner designs reducing weight by 15-30%
- Optimized grinding media composition and size distribution
- Intelligent control systems with real-time adjustment
Featured Retrofitting Technologies
XZM Ultrafine Mill Integration
For operations requiring fine grinding (325-2500 mesh), our XZM Ultrafine Mill delivers exceptional performance:
- 30% lower energy consumption compared to conventional mills
- Precision classification eliminating over-grinding
- Compact footprint reducing installation costs
Technical highlights include:
- Capacity: 0.5-25 t/h (model dependent)
- Special alloy grinding components with 3x lifespan
- Fully automated operation with PLC control
MTW Series Trapezium Mill Upgrades
For medium-fine grinding applications, the MTW Series Trapezium Mill offers:
- 98% efficient gear transmission system
- Curved air channel design reducing energy loss
- Modular wear parts for simplified maintenance
Key specifications:
- Throughput: 3-45 t/h
- Output fineness: 30-325 mesh
- Integrated dust collection system
Case Study: Copper Concentrator Retrofit
A Chilean copper operation achieved:
- 22% reduction in specific energy consumption
- 18% increase in throughput capacity
- 40% decrease in media consumption
- ROI period: 9 months
Why Choose ZENITH?
- State Council-recognized engineering team
- Participation in national standard development
- Global service network across 170+ countries
- Proven track record in 3,000+ installations
Modernizing grinding circuits with ZENITH’s energy-saving solutions provides operators with a clear path to:
- Reduce operating costs by 15-30%
- Extend equipment service life
- Improve product quality consistency
- Meet stringent environmental regulations
Contact our technical team today for a customized retrofit proposal tailored to your specific operational requirements and mineral characteristics.