Common Troubleshooting Guide for High Pressure Suspension Roller Mill Issues
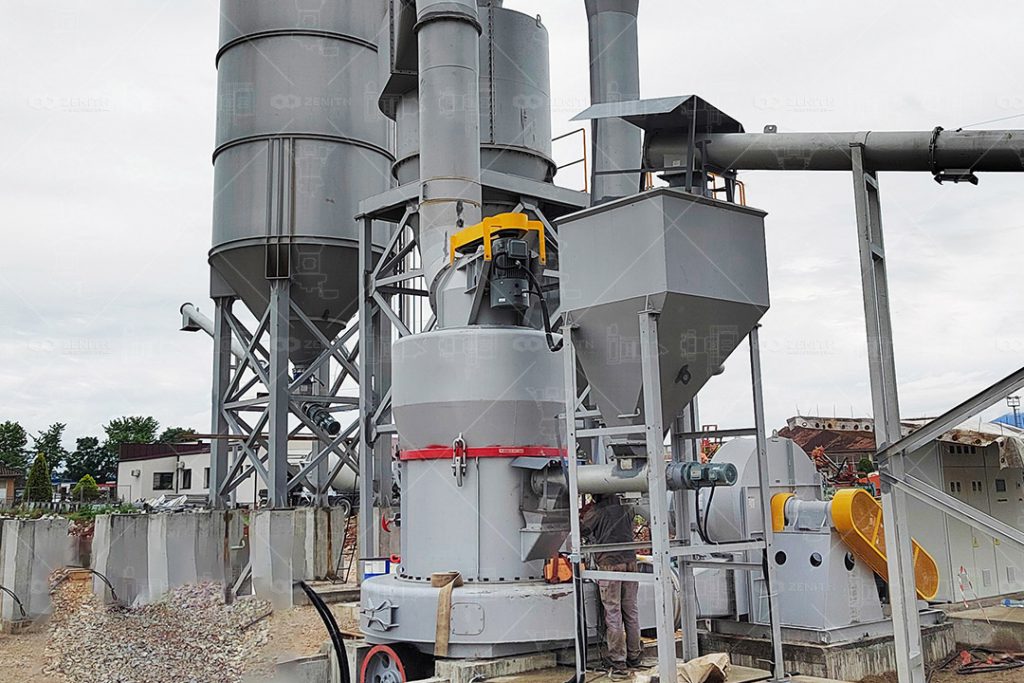
High Pressure Suspension Roller Mills are critical equipment in mineral processing, offering efficient grinding solutions for various materials. However, operational issues may arise due to mechanical wear, improper settings, or material characteristics. This guide provides systematic troubleshooting methods to ensure optimal performance.
1. Insufficient Grinding Pressure
Symptoms
- Reduced production capacity
- Coarse output particles
- Abnormal vibration
Solutions
- Check hydraulic system: Verify oil level and pump pressure (typically 10-12MPa)
- Inspect accumulator: Nitrogen precharge should be 70% of working pressure
- Examine roller surfaces: Replace if wear exceeds 20mm depth
2. Excessive Vibration
Symptoms
- Abnormal noise (>85dB)
- Structural resonance
- Fastener loosening
Solutions
- Material layer check: Maintain 30-50mm thickness
- Dynamic balancing: Tolerance ≤0.5mm/s vibration velocity
- Foundation inspection: Concrete grade ≥C30 required
3. Abnormal Temperature Rise
Symptoms
- Bearing temperature >75°C
- Lubrication oil darkening
- Thermal expansion misalignment
Solutions
- Oil circulation check: Flow rate ≥25L/min
- Cooling system inspection: Water pressure >0.3MPa
- Bearing clearance measurement
4. Product Fineness Deviation
Symptoms
- Inconsistent particle distribution
- D97 tolerance >5%
- Classifier inefficiency
Solutions
- Classifier adjustment: Rotor speed 50-300rpm range
- Airflow optimization: Maintain 5-8m/s in pipes
- Wear parts replacement: Blade tip clearance <3mm
Recommended Solutions from ZENITH
For persistent operational challenges, consider upgrading to ZENITH’s advanced grinding systems:
1. XZM Ultrafine Mill
- Precision grinding: Achieves D97≤5μm
- Energy efficient: 30% lower power consumption
- Smart control: Automatic particle size feedback
2. MTW Series Trapezium Mill
- High capacity: Up to 45ton/h throughput
- Wear-resistant: Combined shovel blade design
- Efficient transmission: 98% gear efficiency
Preventive Maintenance Schedule
Component | Interval | Action |
---|---|---|
Roller bearings | 500h | Grease replacement |
Grinding ring | 2000h | Thickness measurement |
Classifier blades | 1000h | Dynamic balancing |
Conclusion
Proactive troubleshooting combined with ZENITH’s engineered solutions ensures maximum mill availability and product quality. Our global service network provides 24/7 technical support with average response time under 4 hours for critical issues.