50TPH Vertical Roller Mill for Mineral Powder Production – Efficient Grinding Solution
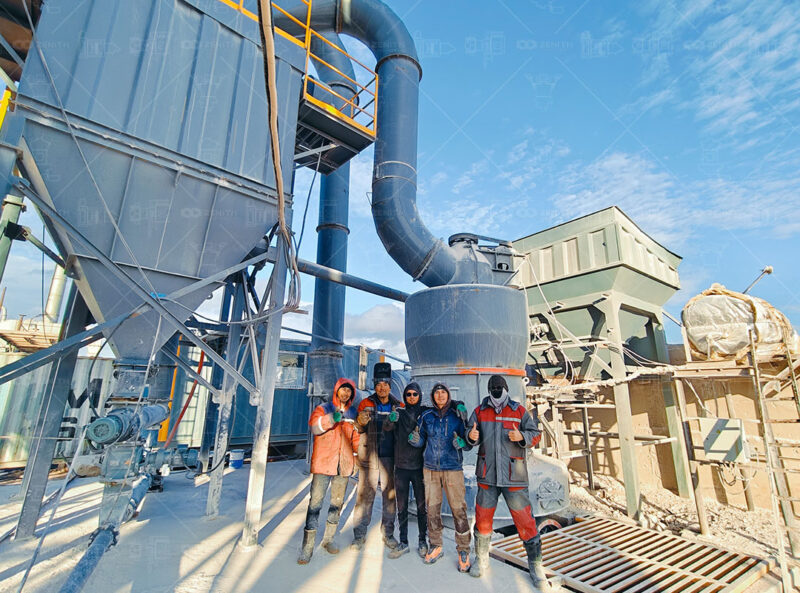
Introduction to Vertical Roller Mill Technology
In modern mineral processing industries, vertical roller mills (VRMs) have become the preferred solution for efficient powder production. With advantages in energy efficiency, space-saving design, and precise particle size control, VRMs outperform traditional ball mills in multiple aspects. This article explores the technical specifications and operational benefits of a 50TPH vertical roller mill system for mineral powder applications.
Key Features of 50TPH VRM Systems
- High Capacity Grinding: Designed for continuous operation with 50 tons per hour throughput capacity
- Precision Classification: Advanced dynamic separators achieve 325-2500 mesh fineness control
- Energy Efficiency: 30-40% lower power consumption compared to conventional systems
- Compact Footprint: Vertical design requires 50% less space than horizontal mills
Technical Specifications
Parameter | Specification |
---|---|
Feed Size | ≤50mm |
Output Fineness | 30-325 mesh (adjustable to 600 mesh) |
Capacity Range | 35-65TPH (standard 50TPH configuration) |
Main Motor Power | 800kW |
Grinding Table Diameter | 2200mm |
Noise Level | ≤80dB(A) |
Recommended ZENITH Products
For clients requiring high-capacity mineral powder production, ZENITH offers two exceptional vertical mill solutions:
1. LM220K Vertical Roller Mill
Our flagship model for medium-to-large scale operations features:
- 50-170TPH processing capacity
- 800kW main motor with frequency conversion control
- Integrated grinding/drying/classification system
- Special alloy grinding rollers with 8,000+ hour lifespan
2. XZM268 Ultrafine Mill
For superfine powder applications requiring 5-25μm fineness:
- 5-25TPH production capacity
- D97≤5μm particle size control
- Vertical turbine classifier for precise size cuts
- Pulse dust collection system with 99.9% efficiency
Operational Advantages
Energy Saving Performance
The VRM’s grinding mechanism operates on the principle of material bed comminution, where particles are crushed between the rotating table and grinding rollers. This method achieves:
- 40% lower specific energy consumption vs ball mills
- Reduced wear part replacement frequency
- Automatic pressure adjustment maintains efficiency
Environmental Compliance
ZENITH’s mills incorporate multiple environmental protection features:
- Fully enclosed negative pressure operation
- Dust emissions <20mg/Nm³
- Low vibration design with noise dampening
- Waste heat recovery options available
Case Study: Calcium Carbonate Production
A recent installation of our LM220K mill for GCC production achieved:
- 52TPH steady output of 325-600 mesh powder
- Specific power consumption of 32kWh/ton
- 98.5% system availability over 12 months
- Return on investment within 18 months
Why Choose ZENITH?
With over 30 years of grinding technology expertise, ZENITH delivers:
- State Council-recognized engineering team
- Participation in national standard formulation
- Global service network across 170+ countries
- Comprehensive after-sales support package
For your mineral powder production needs, contact our technical team to discuss how our vertical roller mill solutions can optimize your operations.