Adjustable Raymond Mill for 80-400 Mesh Powder Production
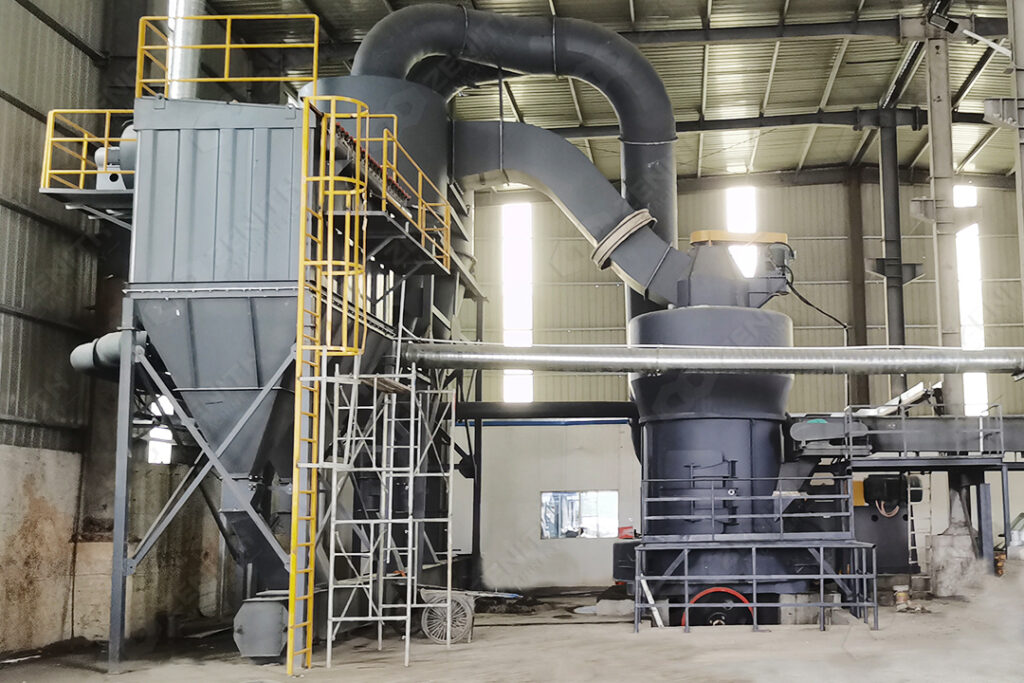
Introduction to High-Efficiency Powder Processing
In modern industrial applications, the demand for finely ground powders ranging from 80 to 400 mesh (180-38μm) has surged across industries like mining, construction, and chemical processing. Adjustable Raymond mills have emerged as the cornerstone technology to meet these precision requirements while maintaining operational efficiency.
The 80-400 Mesh Spectrum: Critical Applications
This specific particle size range serves vital functions:
- Construction Materials: 80-200 mesh powders for cement additives
- Mineral Processing: 200-325 mesh flotation agents
- Chemical Industry: 325-400 mesh catalyst carriers
Technical Challenges in Mid-Range Powder Production
Producing consistent 80-400 mesh powder presents unique technical hurdles:
1. Precision Size Control
Conventional mills struggle with:
- ±15% particle size distribution variations
- Overgrinding of fine fractions
- Incomplete coarse particle elimination
2. Throughput Limitations
Most systems face trade-offs between:
- Production capacity vs. fineness requirements
- Energy consumption per ton
- System uptime vs. maintenance frequency
ZENITH’s Advanced Milling Solutions
With 30+ years of grinding technology innovation, ZENITH has developed specialized mills that overcome these challenges through patented engineering solutions.
Recommended Product: LM Vertical Roller Mill Series
Key Advantages for 80-400 Mesh Production
- Precise Size Control: Dynamic separator with 0.1μm adjustment precision
- High Throughput: 3-250t/h capacity across models
- Energy Efficiency: 30-40% lower kWh/ton than ball mills
- Durable Components: Hardfaced grinding rollers with 8,000+ hour lifespan
Technical Specifications (Selected Models)
Model | LM130K | LM150K | LM170K |
---|---|---|---|
Output Range | 10-28t/h | 13-38t/h | 18-48t/h |
Fineness | 170-40μm (80-400 mesh) | ||
Power Consumption | 5.2-6.8kWh/t | 4.9-6.5kWh/t | 4.7-6.3kWh/t |
Alternative Solution: MTW European Trapezium Mill
Specialized Features
- Curved air duct reduces energy loss by 15%
- Bevel gear transmission (98% efficiency)
- Wear-resistant volute structure
Model Comparison
Model | MTW138Z | MTW175G |
---|---|---|
Capacity | 6-17t/h | 9.5-25t/h |
Fineness | 30-325 mesh (adjustable) | |
Main Motor | 90kW | 160kW |
Operational Best Practices
To maximize performance when producing 80-400 mesh powder:
1. Feed Material Preparation
- Maintain consistent moisture content below 8%
- Pre-crush to ≤20mm for optimal mill feeding
- Implement metal removal systems
2. System Optimization
- Adjust classifier speed for target fineness
- Monitor grinding pressure (typically 8-12MPa)
- Optimize air volume for material transport
Comparative Analysis: Vertical vs. Raymond Mills
Parameter | LM Vertical Mill | Traditional Raymond |
---|---|---|
Energy Efficiency | ★★★★★ | ★★★☆☆ |
Fineness Control | ★★★★☆ | ★★★★★ |
Maintenance Cost | ★★★★☆ | ★★★☆☆ |
Footprint | ★★★★★ | ★★★☆☆ |
Modern adjustable mills like ZENITH’s LM series and MTW trapezium mills provide the ideal solution for 80-400 mesh powder production, combining precision control with industrial-scale throughput. Their advanced designs address the fundamental challenges of mid-range powder processing while delivering superior operational economics.
For operations requiring consistent quality within this critical particle size range, these mills represent the next evolution in grinding technology – offering the perfect balance between Raymond mill precision and vertical mill efficiency.