Ultrafine Grinding Process of Calcium Carbonate for Paper Filling Applications
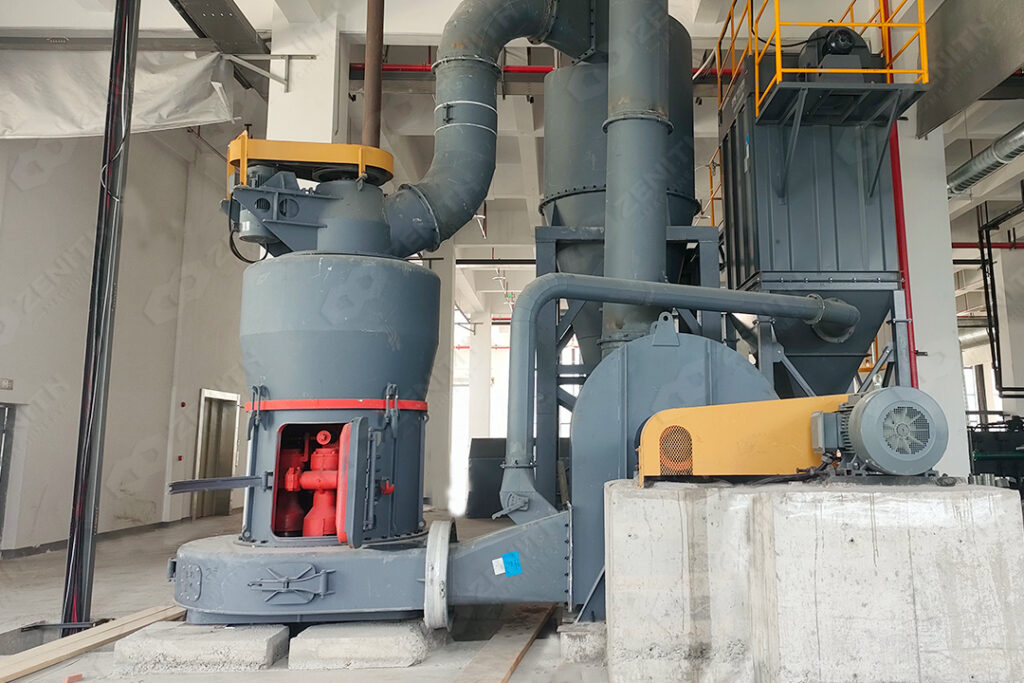
The paper industry extensively utilizes calcium carbonate (CaCO₃) as a filler material to enhance opacity, brightness, and printability while reducing production costs. Achieving optimal particle size distribution through ultrafine grinding is critical for maximizing paper quality and process efficiency. This article explores the technological advancements in calcium carbonate ultrafine grinding, with a focus on solutions tailored for paper filling applications.
Technical Requirements for Paper-Grade CaCO₃
Particle Size Specifications
Paper manufacturers typically require:
- Coated paper: D90 ≤ 2μm (90% particles under 2 microns)
- Uncoated paper: D97 ≤ 10μm
- Narrow size distribution: Span value (D90-D10)/D50 < 1.5
Key Performance Indicators
Parameter | Target Value |
---|---|
Brightness (ISO) | ≥ 94% |
Oil Absorption | 20-35g/100g |
Specific Surface Area | 5-15 m²/g |
Grinding Technology Comparison
Conventional vs. Ultrafine Grinding
Traditional ball mills achieve only 45-75μm (200-325 mesh), whereas modern ultrafine systems can produce:
- XZM Ultrafine Mill: 5-45μm (325-2500 mesh)
- LUM Vertical Mill: 5-30μm (D97 control)
Recommended Solution: XZM Ultrafine Mill
For paper filling applications, ZENITH’s XZM Ultrafine Mill demonstrates exceptional performance:
Technical Highlights
- Precision Classification: Vertical turbine classifier achieves 99.9% classification efficiency
- Energy Efficiency: 30% lower power consumption vs. jet mills
- Paper-Specific Optimization: Special grinding curve design prevents particle agglomeration
Case Study: Coated Paper Production
A European paper mill achieved:
- Production increase: 22% higher machine speed
- Quality improvement: 3-point brightness enhancement
- Cost reduction: €18/ton savings in binder usage
Process Flow Optimization
Integrated Grinding System
- Primary crushing: Hammer mill to ≤20mm
- Intermediate storage: Moisture control to <1%
- Ultrafine grinding: XZM system with closed-circuit air classification
- Surface modification: Stearic acid coating (optional)
Alternative Solution: MTW Trapezium Mill
For operations requiring broader particle distribution, ZENITH’s MTW Series Trapezium Mill offers:
Advantages for Filler Production
- Dual-purpose operation: 30-325 mesh adjustable output
- High throughput: Up to 45 ton/hour capacity
- Wear-resistant components: 3,000+ hour maintenance interval
Quality Control Measures
Critical Process Parameters
Parameter | Control Range |
---|---|
Grinding Temperature | <85°C |
Classifier Speed | 800-1500 rpm |
System Pressure | -500 to -800 Pa |
Modern ultrafine grinding systems like ZENITH’s XZM and MTW mills enable paper manufacturers to achieve superior filler quality with operational efficiency. The integration of precision classification, energy-efficient design, and process automation ensures consistent production of paper-grade calcium carbonate that meets stringent industry requirements.
About ZENITH
With over 30 years of experience in grinding technology, ZENITH has supplied more than 500 mineral processing systems worldwide. Our R&D team, led by State Council-subsidized engineers, continuously develops innovative solutions for the paper industry. The company maintains 30+ overseas offices to provide localized technical support and after-sales service.