Vertical Roller Mill for Steel Slag Micro Powder Production: Key Features and Benefits
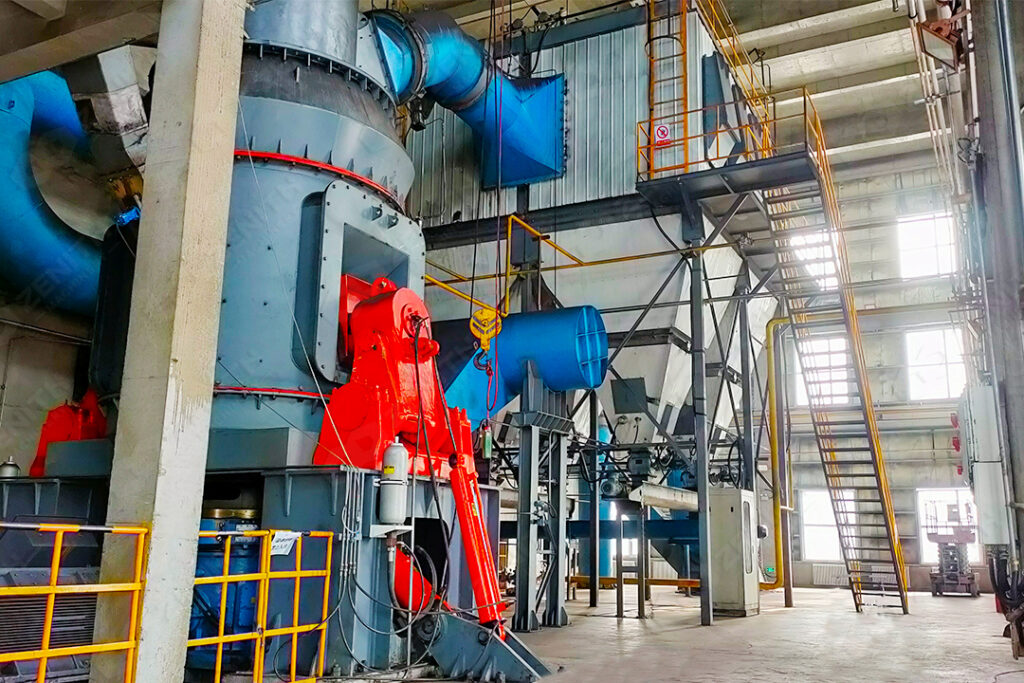
Introduction to Steel Slag Micro Powder Production
Steel slag, a byproduct of steelmaking, has long posed environmental challenges due to its disposal. However, with advanced grinding technologies, it can be transformed into high-value micro powder for applications in cement production, road construction, and soil improvement. Vertical roller mills (VRMs) have emerged as the most efficient solution for steel slag micro powder production, offering superior energy efficiency and particle size control compared to traditional ball mills.
Technical Advantages of Vertical Roller Mills
1. Energy Efficiency
VRMs consume 30-50% less energy than conventional ball mills due to their innovative grinding mechanism. The material is ground between rollers and a rotating table, requiring less power for the same output.
2. Precise Particle Size Control
Integrated dynamic classifiers in VRMs enable precise control over particle size distribution, crucial for steel slag applications where specific surface area (420-450 m²/kg) determines reactivity.
3. High Capacity
Modern VRMs can process up to 110 t/h of steel slag, with our LM370N model setting industry benchmarks for large-scale production.
4. Low Maintenance
Wear parts in VRMs last 3-5 times longer than in ball mills, with our proprietary roller and table lining materials demonstrating exceptional durability against steel slag’s abrasive nature.
ZENITH’s Vertical Roller Mill Solutions
With over 30 years of experience in grinding technology, ZENITH has developed specialized VRMs for steel slag processing:
Recommended Product: LM Vertical Slag Mill Series
- Model Range: LM130N to LM370N
- Capacity: 4-110 t/h
- Final Fineness: ≥420 m²/kg
- Moisture Content: ≤1%
Our LM220N model stands out for medium-scale operations with:
- 20-26 t/h production capacity
- 900-1000 kW power requirement
- 2800mm grinding table diameter
- Integrated drying for slag with ≤15% moisture
System Components and Operation
1. Feeding System
Equipped with metal detectors and belt scales to ensure consistent feed rates of ≤50mm slag particles.
2. Grinding Zone
Our patented roller design applies optimal pressure (50-150 N/mm²) to create efficient bed comminution.
3. Classification System
High-efficiency rotor classifiers achieve precise cuts at 325-600 mesh with minimal energy consumption.
4. Dust Collection
Pulse-jet bag filters maintain emissions below 20 mg/Nm³, exceeding international environmental standards.
Case Study: Successful Steel Slag Processing
A Chinese steel plant achieved 98% utilization of their slag byproduct after installing our LM190N mill, producing:
- 450,000 t/year of slag powder
- 28 kWh/t specific energy consumption
- 430-450 m²/kg Blaine fineness
Vertical roller mills represent the future of steel slag valorization, combining environmental benefits with economic returns. ZENITH’s LM series offers the most advanced technology for this application, backed by our global service network and 30 years of grinding expertise.
For operations requiring ultra-fine slag powder (D97 ≤ 5μm), we recommend our XZM Ultrafine Mill as a complementary solution, capable of producing 325-2500 mesh powder with exceptional energy efficiency.