Vertical Mill for Dry Grinding of Steel Slag: Efficient Processing Solution
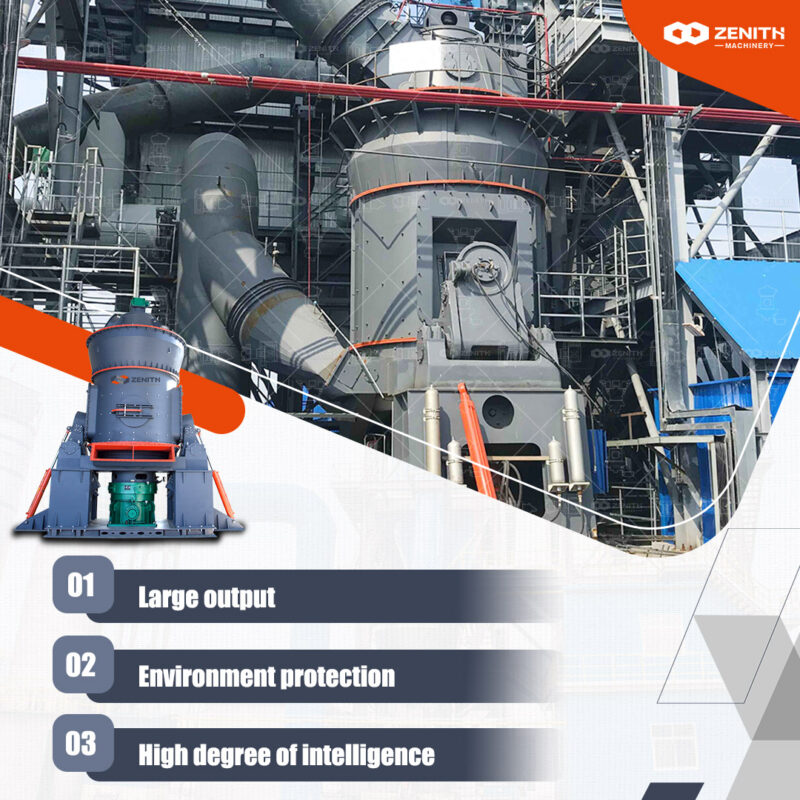
Introduction to Steel Slag Processing
Steel slag, a byproduct of steelmaking, presents both environmental challenges and economic opportunities when properly processed. Dry grinding technology has emerged as the preferred method for transforming this industrial waste into valuable construction materials like cement additives or road base aggregates. Vertical roller mills (VRMs) have proven particularly effective in this application due to their energy efficiency and precise particle size control.
Technical Advantages of Vertical Mills for Slag
1. Energy Efficiency
Modern vertical mills consume 30-40% less energy compared to traditional ball mill systems. The material layer grinding principle significantly reduces power consumption while maintaining high throughput.
2. Precise Particle Size Distribution
Integrated dynamic classifiers in VRMs enable production of slag powder with consistent fineness (typically 420-450m²/kg Blaine), meeting strict requirements for cement replacement applications.
3. Moisture Tolerance
Advanced drying capabilities allow processing of slag with moisture content up to 15% without pre-drying, reducing overall system complexity.
ZENITH’s LM Vertical Slag Mill Series
As a pioneer in mineral processing equipment, ZENITH offers specialized solutions for steel slag recycling through our LM Vertical Slag Mill series. These mills combine German engineering with localized manufacturing advantages, delivering exceptional performance in demanding industrial applications.
Key Features:
- High Capacity: Models ranging from 4t/h to 110t/h production capacity
- Precision Grinding: Guaranteed product fineness ≥420m²/kg
- Robust Construction: Specially hardened grinding components for abrasive materials
- Intelligent Control: PLC-based automation system with remote monitoring
Recommended Product: LM220N Vertical Slag Mill
For medium-to-large scale steel slag processing plants, we particularly recommend our LM220N model:
Parameter | Specification |
---|---|
Grinding Capacity | 20-26 t/h |
Main Motor Power | 900-1000 kW |
Feed Size | ≤50mm |
Product Fineness | ≥420m²/kg |
Moisture Content | ≤1% in final product |
System Integration
The complete slag grinding system typically includes:
- Raw material feeding system with metal detector
- Vertical slag mill with hot air generator
- High-efficiency dynamic classifier
- Pulse jet bag filter (emission <20mg/Nm³)
- Product conveying and storage system
Case Study: Successful Application
A steel plant in Hebei Province, China achieved remarkable results after installing ZENITH’s LM190N vertical slag mill:
- Annual processing capacity: 80,000 tons of steel slag
- Energy savings: 38% compared to previous ball mill system
- Product quality: Consistently meeting GB/T 18046-2017 standard for slag powder
- ROI period: Less than 2 years
Alternative Solution: MTW Series Trapezium Mill
For smaller-scale operations or when processing slag with higher moisture content, our MTW215G Trapezium Mill presents an excellent alternative:
Parameter | Specification |
---|---|
Grinding Capacity | 15-45 t/h |
Main Motor Power | 280 kW |
Feed Size | ≤50mm |
Product Fineness | 10-325 mesh adjustable |
Vertical roller mills represent the most advanced technology for dry grinding of steel slag, offering superior energy efficiency and product quality. ZENITH’s extensive experience in mineral processing equipment ensures reliable, high-performance solutions tailored to each customer’s specific requirements. Our global service network provides comprehensive support from project planning to after-sales maintenance.
For steel plants and slag processors looking to maximize the value of their byproducts while meeting environmental regulations, investing in modern vertical grinding technology delivers both economic and ecological benefits.